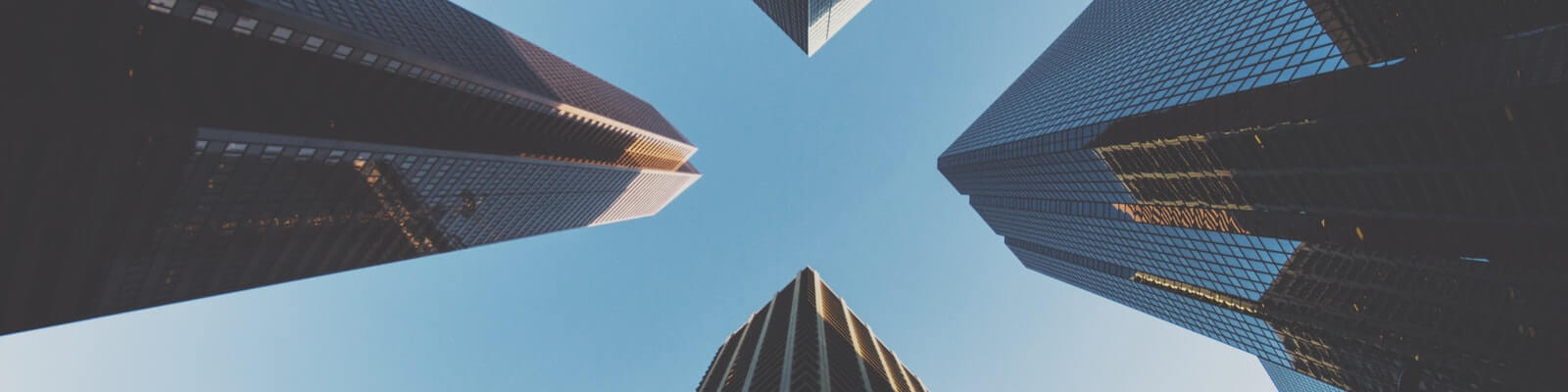
Productivity Through People
A ten-month programme in partnership with three world class manufacturers; BAE Systems, Siemens and Rolls-Royce, designed to support and invest in the key decision-makers of tomorrow. Gain access to the latest techniques, thinking and research to transform your productivity and working practices.
About the Programme
This is a historic programme that was subsidised by BAE Systems, Siemens and Rols Royce between 2016 and 2020. For further information about other business development opportunities please get in touch with us.
You'll begin with a Programme Induction, which is a two-day event made up of leadership exercises, focused discussions and peer-to-peer learning. Taking the time away from your workplace, you'll be encouraged to think about your business differently and reflect on your current practices. This experience is designed to develop trust amongst the participants, breaking down the barriers to learning and providing opportunities to connect your new knowledge to real-life situations.
Following this, you'll participate in a series of elements to develop your knowledge and skills as well as an unparalleled opportunity to meet key people from leading UK organisations where excellence in productivity lies at the heart of business. You will have access to gold standard manufacturing organisations including BAE Systems, Siemens and Rolls-Royce. These companies will demonstrate how they have transformed their workplace by putting employee engagement at the very centre of their improvement processes.
Productivity through People workshops will initially be delivered online with a view to move to face-to-face workshops when this is safe to implement.
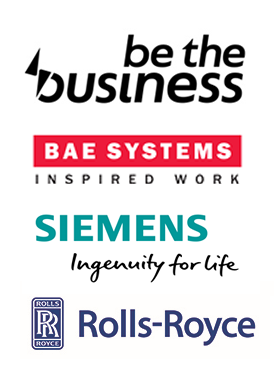
Programme Elements
Productivity through People includes two non-consecutive days each month, after the initial Programme Induction, to develop your leadership & management capabilities to empower your workforce. You'll participate in a range of online workshops including a variety of challenges and tasks to develop the tools and techniques to transform your productivity and working practices. The focus on practical learning means there are no formal assessments. You may need to do some pre-reading, and you'll be expected to contribute via the online forum.
The Benefits
This programme will help you to empower and engage front line staff leading to better usage of skills and abilities, transforming management practices and developing leadership skills. You will develop a support network of other SME owner/managers to build a more productive future together, and the exposure to world-class manufacturing environments will enable you to formulate high-performance workplace strategies.
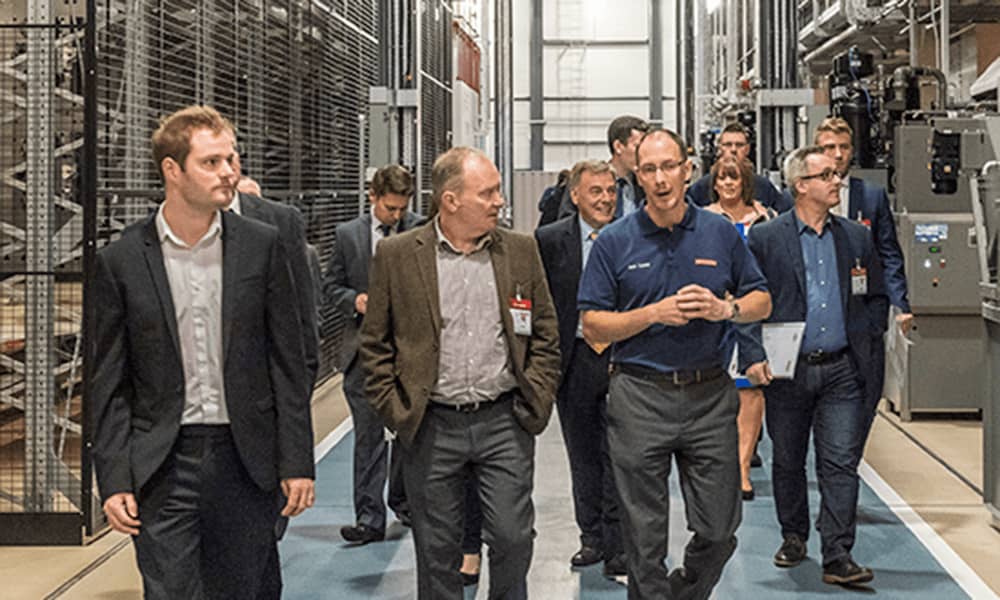
Driving Growth in NW SMEs by Solving the Productivity Puzzle
Understanding what drives productivity growth is vital to tackle the UK’s “productivity puzzle” and to exploit the opportunities presented by Industry 4.0. Lancaster University’s expertise in the productivity agenda is making Lancashire the place for people based productivity solutions – and its key deicison-makers of North West SMEs that are feeling the benefits.
Read article"Many businesses have been hit very hard by the pandemic. For some it created a stressful and chaotic environment for leaders and staff as they responded to the changes, accommodating increased production or pivoting their business models. The PtP programme provides businesses with a structured approach to creating a sustainable business, which will offer crucial support that is particularly important during these challenging times.”
Helen Wilkinson, Knowledge Exchange Manager
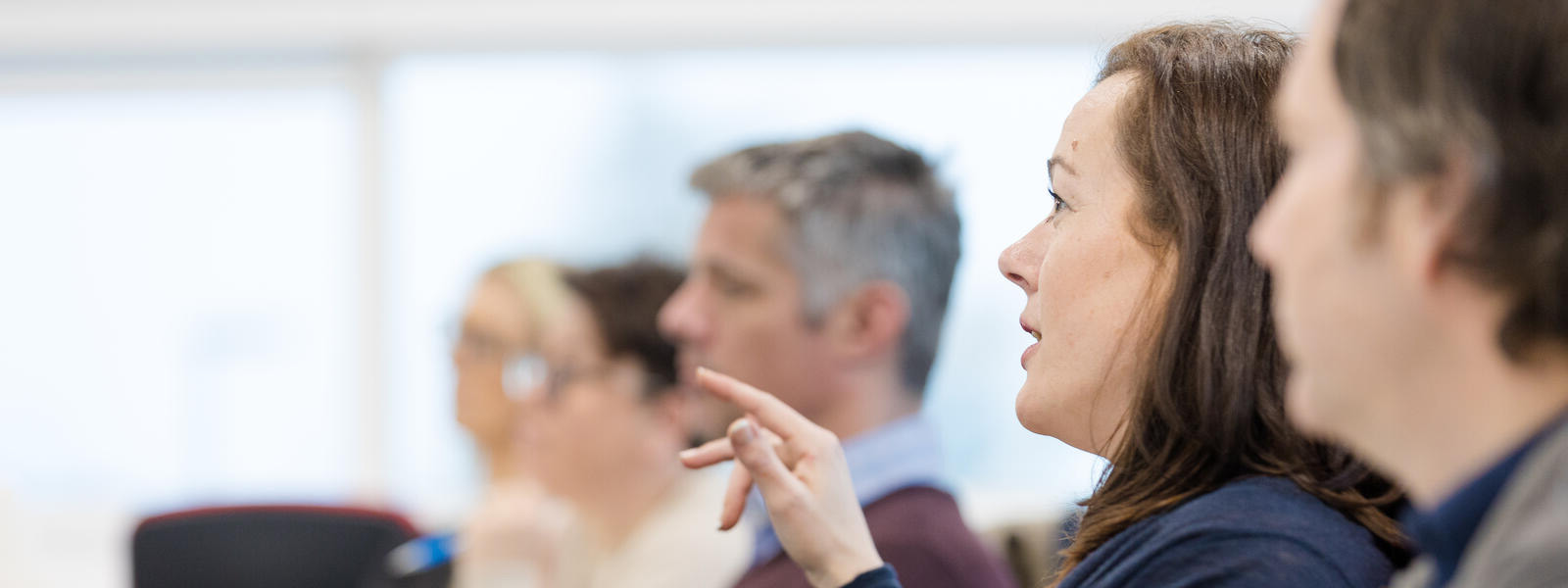
Costs & Apply
This programme has received significant investment from the industrial partners, both in its design and finance. As a result the subsidised cost of this programme is £2,500 per delegate.
Find out more about how and why Lancaster University hold your information.
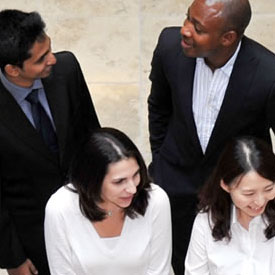